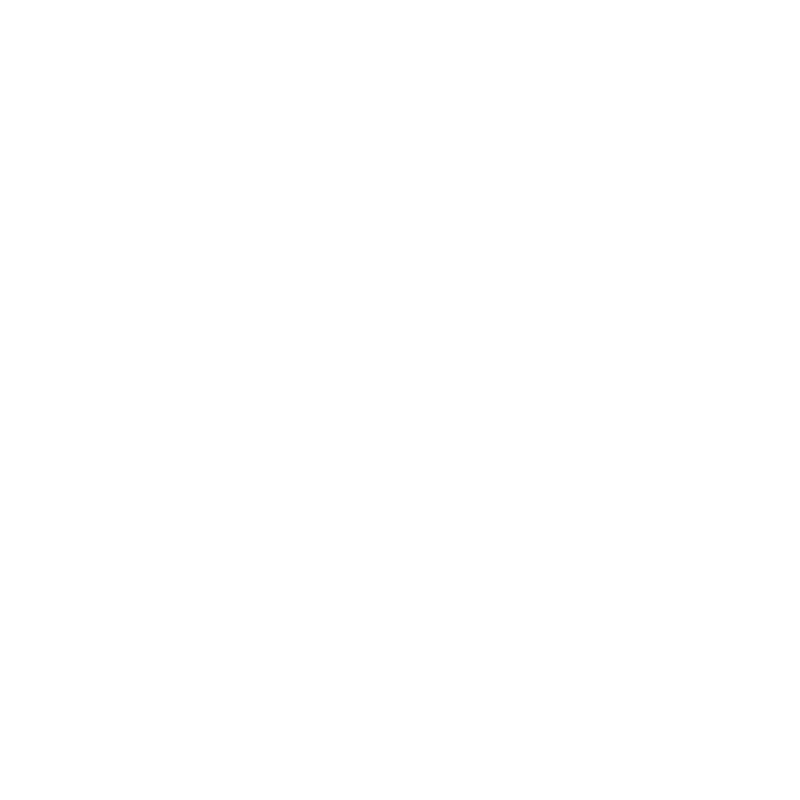
The CNC five-axis machining center combines high speed and high rigidity, multi-angle and multi-dimensional machining technology, and one-time clamping to complete the production and processing requirements of complex curved surfaces in one go, thereby improving production efficiency and production accuracy. With the demand for intelligent production, five-axis machining centers are widely used in the production of aerospace, rail transportation, and new energy.
Compared with three-axis machining centers, the popularity and utilization rate of five-axis machining centers in the market is still relatively low. Many people don’t know what the five axes of a five-axis machining center are. Generally speaking, the five axes of a five-axis machining center include three linear axes X, Y, and Z and two rotary axes A and B, which can meet the processing needs of various products.
The use of a rotary axis on a five-axis machining center means that the machine can move the part or cutting tool (spindle head) around one of the previously established linear axes. Different machining equipment will use different combinations of axes, with each configuration suited to different types of machining.
The five-axis machining process is also very similar to the three-axis CNC machining process, but it has two additional rotational axes, providing greater cutting flexibility. In a five-axis machining center, the spindle and tool move along three axes, while there is rotation around the X-axis (A-axis), Y-axis (B-axis), and Z-axis (C-axis). Which two rotational axes are used depends on the configuration of the machine.
There are many advantages to the use of a five-axis machining center. First, it enables the use of shorter cutting tools because the head can be lowered and directed toward the workpiece surface. This allows for higher cutting speeds, longer tool life and less breakage. In addition, using shorter tools also reduces tool vibration that can result when machining deep cores or cavities using a three-axis machine. This results in a higher quality surface finish, reducing or even eliminating the need for manual finishing.
Secondly, a five-axis machining center can machine extremely complex parts from solid objects, avoiding the need for casting. Especially for prototypes and very small runs, this machining method is faster and cheaper. Compared to a casting that takes two months or more, a five-axis machining center can deliver it in one to two weeks.
In addition,
a five-axis rotary machining center can also save a lot of drilling time. Although drilling a series of holes with different compound angles may seem trivial, it is actually very time-consuming. If a three-axis machine is used, setting different process parameters for each hole is a must. With a five-axis machining center, the head can be automatically oriented along the correct axis for each hole, greatly speeding up drilling.
In general, five-axis machining centers are widely used in aerospace, rail transportation, new energy and other fields due to their multi-axis, high rigidity, high speed, and one-time clamping and one-time processing capabilities.